Get in Touch with Our Statistics Experts
Fill out the form below, and our team will get back to you shortly.
Timeline Process
Data Collection
Collect inventory data, including stock levels, sales history, reorder points, and lead times to understand the flow of products within the system.
Data Cleaning and Preparation
Clean and preprocess the data by handling missing values, removing duplicates, and ensuring consistency in the inventory records for analysis.
Demand Forecasting
Analyze historical demand data to predict future sales and inventory needs, helping to determine optimal stock levels and reorder frequencies.
Stock Optimization
Use inventory optimization techniques like Economic Order Quantity (EOQ) or Just-In-Time (JIT) to ensure inventory levels are balanced between overstock and stockouts.
Replenishment Strategy Development
Develop a replenishment strategy based on demand forecasts and lead times to ensure timely restocking of inventory while minimizing costs.
Inventory Monitoring
Implement a system to continuously monitor inventory levels, track product movement, and update stock data in real time for more accurate management.
Reporting and Recommendations
Prepare a report summarizing the inventory management strategies, performance, and provide recommendations for improving efficiency, reducing costs, and optimizing stock levels.
Submit Your Request
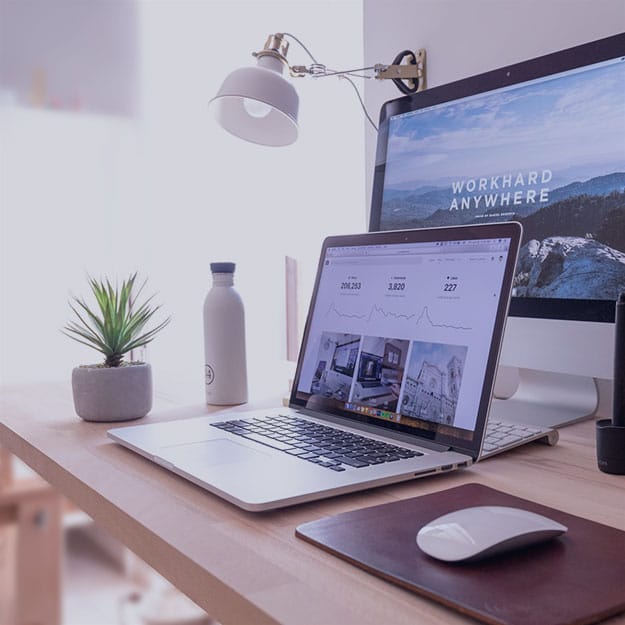